XY Stage for High Speed Hematology Instrument
Our monolithic XY system increased the speed and reliability of the imaging within this blood analysis instrument without a large cost increase.
At a Glance
- A client needed a faster and more reliable XY system for a client’s hematology instrument
- Previous iterations had used a screw driven stage that was not delivering the results they needed
- We worked closely with the client to develop a monolithic XY system that fit within the already-designed instrument that achieved all their motion goals
- The resulting motion system was 7.5 times faster than initial prototypes and came in at half the cost of competitors’ quotes
Precise Movement for Automated Solutions
Our client was working with a global diagnostics company to create their next generation blood analysis instrument. The goal was for the instrument to automate cell morphology analysis, typically a manual process, by using high speed imaging to produce faster and more reliable results.
Following CBC analysis, blood samples flagged for further testing are transferred via conveyor and loaded into this instrument. Blood smears from each sample are then automatically mounted on individual slides and positioned beneath a fixed microscope by an XYZ stage. It was this automated, precise and quick movement of the blood sample beneath the microscope that needed Dover Motion’s precision motion expertise.
The Backlash of Screw Driven Motors
Initial prototypes of the instrument had used a fine-pitch screw driven stage that was not meeting performance targets. Using a fine-pitch screw driven motor can supply small and precise movement, but will take a very long time. Conversely, a larger pitch screw motor will supply speed but without achieving high resolution.
There was also the issue of backlash with the screw driven technology, which had been problematic in early iterations of the instrument. In such a high-speed imaging application, time could not be wasted correcting the overshoot of the motor so that the fixed microscope could focus on the sample.
The instrument's new XY stage with higher speed, repeatability, and reliability would not have any notable increase on the client’s cost. The XY also needed to fit within the chassis without adding a considerable amount of footprint to the instrument that had already been designed.
A Fine-Tuned Direct Drive System
We worked closely with the client to get a full understanding of the issues they were having with the prototype technology, and to understand the environment the stage would be operating under. We removed the screw driven motors from the instrument and built a monolithic, direct drive XYZ motion system from modified versions of our MMG stages to achieve the team’s motion goals. It was the speed, performance accuracy, and repeatability of motion that made direct drive technology the best fit for this challenge.
The reduced profile of the monolithic configuration allowed us to fit the stage within the existing instrument framework, and provided a consistent and repeatable manufacturing and setup process. It also assisted in the servo tuning of the system by having one set of parameters for all instruments rather than having to fine tune each stage.
Direct drive motors without proper servo tuning can have prolonged settle time with their movements, and any unwanted movement in an imaging application causes the objective to be unable to focus. We provided both the stages and the motion controller for this instrument. Because of this, we could use our knowledge about the environment the instrument would be in to tune each motion system to perfection before we shipped them to the client ensuring they were ready for operation upon arrival.
The XY stage and the Z axis motion assembly were mounted within a rigid, co-developed, cast metal frame that integrated into the instrument structure. Dover Motion fully tested and servo tuned the imager axes, so there was no additional customer functional testing needed.
The Dover Motion Difference
We delivered a customized motion control subsystem in less than 8 weeks that:
- Provided XY movement that was 7.5 times faster than the initial prototypes, moving 880 microns in 80 milliseconds with 10 microns of settle
- Decreased the backlash from 1.2 um to .1 um
- Increased the repeatability by 50%
The overall result was a faster, more reliable, more compact instrument that provided higher throughput at a lower cost that was half as much as competitors’ quotes.
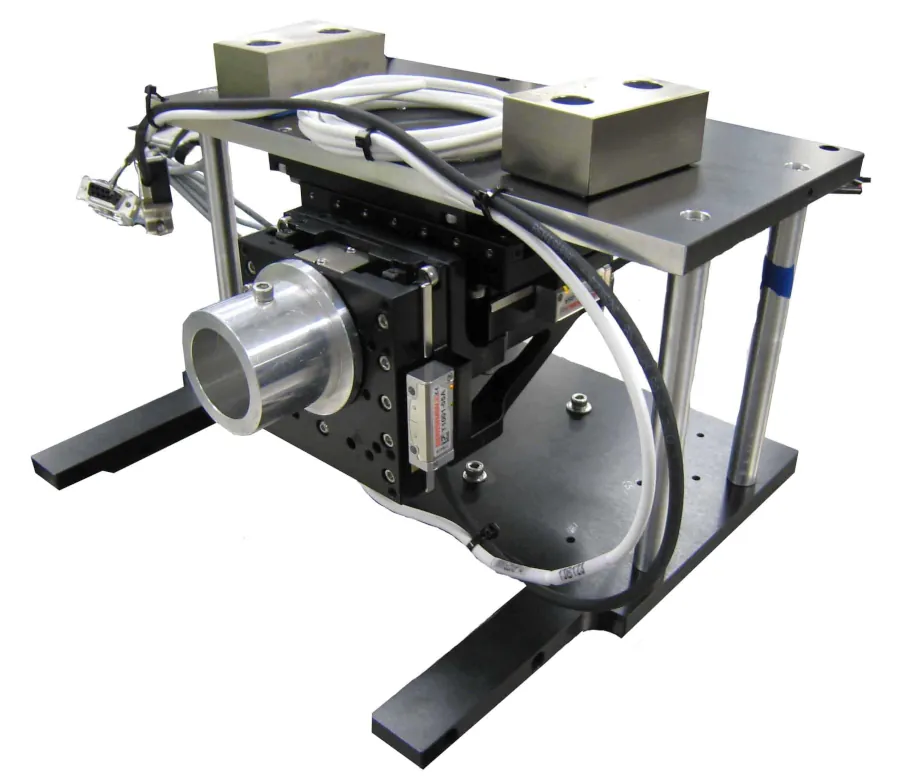
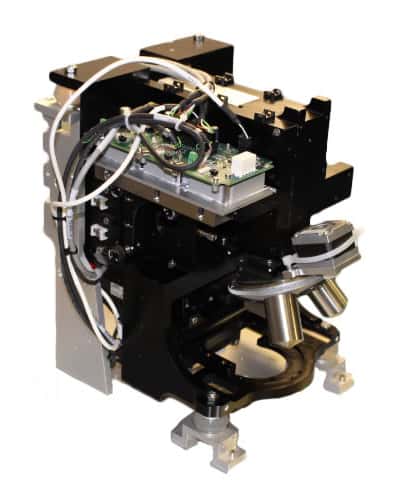