Motorized Stages
A motorized stage is a device used in various life science applications to move objects in a controlled and precise manner. The motorized stage consists of a platform that can be moved along one or more axes using motors and mechanical components.
Dover Motion's motorized stages include motorized translation stages with up to 635 mm of travel, motorized XY stages, vertical Z stages, and microscope stages. Each motorized stage features stepper and servo single and multi-axis motors, built-in motion controllers, and optimal travel time for precision motion. As a leader in creating motion solutions for the life sciences industry, we also specialize in manufacturing standard and custom motorized optical stages that meet higher precision and accuracy requirements for use with optical instruments, including microscopes and cameras.
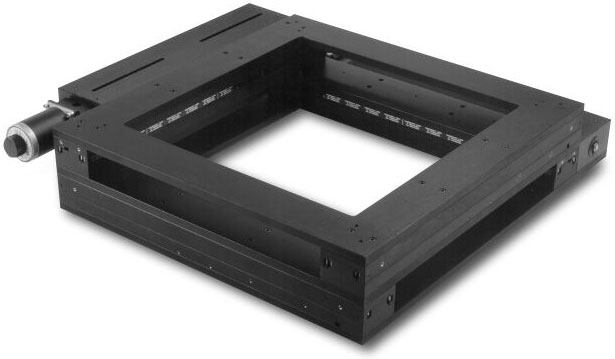
Motorized Stage Products
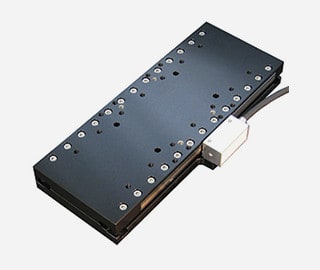
Let's Explore
Overview
Our direct drive linear motor stages include linear servo motors and offer higher speed, acceleration, and accuracy than belt-drive, lead screw, or rack and pinion actuators.
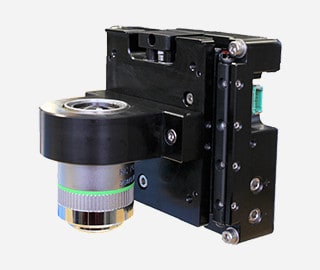
Let's Explore
Overview
Our Z stages offering includes traditional Z stages for objective focusing and Z stages for sample positioning or Z-Lift stages .
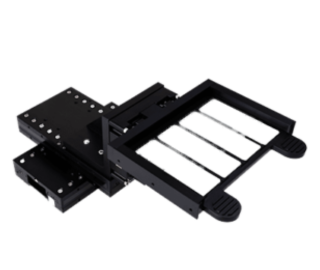
Let's Explore
Overview
Our microscope stages are made with embedded high-performance precision electronics required to control motion within the stage without increasing its size.
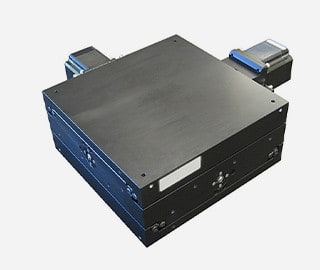
Let's Explore
Overview
Our XY stages include high performance, open frame, monolithic high load, and custom designed XY stages that move in two degrees of freedom and offer high precision and efficiency for digital imaging applications.
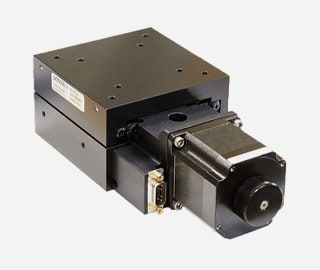
Let's Explore
Overview
Our screw driven motorized stages range from stages with monolithic integrated XY centers to low-cost, single axis stages with crossed roller ways and stepper motors.
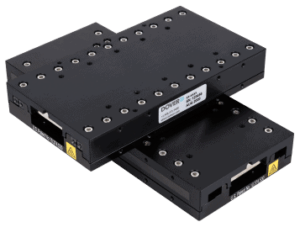
Let's Explore
Overview
The SmartStage™ XY motorized stage features a built-in motion controller, ONE external cable and has a 5 nm resolution with 0.8 um bi-directional repeatability.
See How We are Disrupting Motion Control
Our innovative precision motorized stages have been winning industry awards

Motorized Stage Guide
Motorized stages play a critical role in achieving high accuracy and efficiency in various applications, from scientific research to industrial automation. Yet, information on choosing the right motorized stage is not widely accessible. Our guide aims to provide a comprehensive overview, addressing common questions and highlighting key features to help you select the stage that best fits your application.
What is a motorized stage?
A motorized stage is a high-performance positioning system that utilizes integrated motors to drive a platform with exceptional accuracy along one or more linear axes. These stages are instrumental in various automated applications across science and industry, particularly those requiring meticulous object manipulation.
The motorized stage provides precise automated positioning and is available in single or multi-axis architectures. It is also commonly referred to as a motorized table or motorized actuator. Each axis of a motorized stage must constrain the six degrees of freedom (X, Y, Z, roll, pitch, and yaw) of the payload to only one, producing automation along a single axis of motion. This is accomplished with a set of linear bearings, which are mounted to a metal base to provide a stiff structure. Our stages designed specifically for vertical motion can be viewed on our Z Stages page.
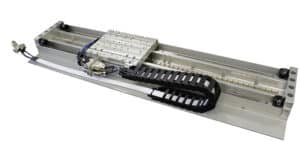
How does a motorized stage work?
Once the payload has been constrained to a single degree of freedom, the system’s next mission is to actuate the payload and provide precise incremental linear motion along the guideway.
Linear actuator methods include:
- Friction screws with anti-backlash nuts
- Ball screws
- Belt and pulley
- Rack and pinion
- Piezo actuators
- Linear motors
Using a linear motor is generally considered to be optimal for high speed motion systems and is the most precise and repeatable linear motion actuation technology.
A motorized stage with a linear motor requires a linear feedback device as well as a servo drive and control to close a position feedback loop. With a high-resolution linear encoder, linear actuators can provide position control down to the nanometer level. A typical application for high precision linear actuators is to control the focus of a microscope objective in a digital imaging system.
Types of Motorized Stages
- Linear Stages. Linear stages provide straight-line motion and are commonly used in microscopy and gene sequencing applications. The most common types include screw-driven, direct-driven, and multi-axis stages.
- Rotary Stages or Rotation Stages. Rotary stages enable rotational movement, which is required in applications such as optical alignment and cellular imaging. They offer high precision and can be motorized with stepper or servo motors.
- XY Stages. XY stages provide two-dimensional movement and are ideal for tasks requiring precise control in both the X and Y axes. We widely use these stages in digital imaging.
- Vertical Z Stages. Vertical Z stages offer movement along the Z-axis, making them perfect for focusing applications in microscopy and automated liquid handling systems.
Applications of Motorized Stages
Motorized stages are versatile and find applications in various fields, including:
- Scientific Research: For precise sample positioning in microscopy and spectroscopy.
- Semiconductor Manufacturing: For wafer inspection and alignment.
- Bio-medical Research: For automated liquid handling and sample analysis.
- Industrial Automation: For precise control in assembly lines and robotic systems.
Advantages of Motorized Stages
- High Precision: Achieve nanometer-level accuracy with advanced feedback systems.
- Automation: Enhance productivity by automating repetitive tasks.
- Versatility: Suitable for a wide range of applications across different industries.
- Customization: Tailor-made solutions to meet your specific requirements.
Choosing the Right Motorized Stage
When selecting a motorized stage, consider the following factors:
- Load Capacity: Ensure the stage can handle the weight of your payload.
- Travel Range: Determine the required travel range for your application.
- Precision: Choose a stage with the necessary accuracy.
- Speed: Consider your project’s speed requirements.
Key Components of a Motorized Stage
A typical motorized stage consists of several key components:
-
Motor: The motor is the driving force behind the stage's movement. It converts electrical energy into mechanical energy to move the stage platform.
-
Drive Mechanism: The drive mechanism transmits the motion from the motor to the stage platform. It can be a screw drive, belt drive, or direct drive system.
-
Controller: The controller is responsible for controlling the motor's speed, acceleration, and position. It receives input signals from sensors and actuators and generates appropriate control signals to achieve the desired motion.
-
Sensors: Sensors are used to measure the stage's position, velocity, and acceleration. They provide feedback to the controller, allowing it to maintain precise control over the stage's movement.
How does a linear motor stage differ from a screw-driven stage?
Linear motor stages offer higher speed and precision, while screw-driven stages are more cost-effective and suitable for less demanding applications.
What is a motorized optical stage?
A motorized optical stage is a stage that is designed for use with optical instruments such as microscopes or cameras and is moved by a motor. It provides precise control over the position and movement of samples and optical components. The motorized optical stage has higher precision and accuracy requirements than the general motorized stage, as the movement of the sample or component needs to be very precise for accurate imaging or analysis. Some motorized optical stages have additional features such as encoder feedback for closed-loop control, joystick or computer control, and programmable motion profiles, which are specific to optical applications.
At Dover Motion, we specialize in designing and manufacturing motorized optical stages that meet the highest standards of accuracy and reliability. Our stages are designed to deliver smooth, stable motion with sub-micron positioning accuracy, even in harsh environments or challenging applications. They range from single-axis stages for simple applications to multi-axis systems for complex processes and are available in a variety of sizes and configurations, with options for linear or rotary motion. Our experienced team of engineers works closely with our customers to understand their specific requirements and design custom motorized optical stages that are tailored to their unique needs.
What is a translation stage with a motor?
A translation stage with a motor is a precision mechanical device used in motion control applications that allows for precise linear movement along single or multiple axes. The motor is used to drive the translation stage, providing smooth and precise motion control. Translation stages with a motor are commonly used in scientific research, bio-medical, life sciences, metrology, semiconductor, precise manufacturing, and other industries where precise positioning is required.