Precision Motion Control
Precision Motion Control
Dover Motion can address the performance requirements of your most demanding applications that require precision motion control and has over six decades of experience designing precision linear stages, rotary stages, and complete precision motion control systems.
Our skillset in precision motion control includes:
- Precision surface grinding, both pre- and post-hard coating
- The use of advanced materials such as alumina ceramics, carbon-fiber, Zerodur, and diamond-like carbon
- Structural exterior and interior light-weighting for maximum stiffness/mass ratio
- Skills in the use of cutting-edge position and angle metrology instrumentation
- 2-D and 3-D software compensation of residual stage errors
- In-house design of both ironless and iron-core linear servo motors
- Expertise in control theory and the design of high-performance servo loops
- In depth knowledge of precision motion control system design
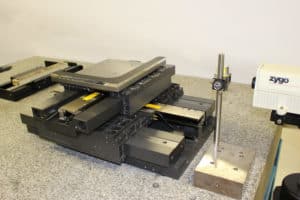
Precision Motion Control Stages
High precision motion control positioning stages serve a wide array of applications and can be considered “high precision” for various difference reasons. For some stages, it is critical to minimize geometric errors and provide true XY accuracy within the working area or volume. In other cases, one or more precision motion axes are required to move with exceptionally constant velocity. These systems often require that periodic triggers be generated at extremely precise positions, and that encoder cyclical error be eliminated.
In other applications, minimizing position jitter when stopped is paramount with permissible jitter being only a few nanometers. This requirement is often coupled with a need to move very quickly from position to position (see Figure 2). For yet finer position stability, Coulomb friction can be engaged, reducing jitter to 10 to 20 picometers.
Dover Motion has extensive experience in providing precision motion control solutions configured to fit many different applications and can address even the most challenging requirements.
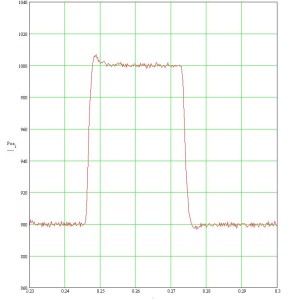
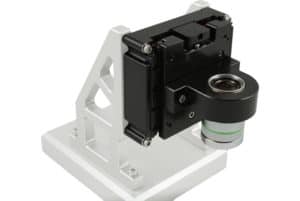
In the last 50 years, there have been amazing advances in the precision motion components that we leverage to deliver high performance precision stages to our customers. Linear optical encoders have increased their resolution by over six logs, shrinking from 25 microns to 10 picometers. For many years, linear amplifiers in a precision linear stage were the only solution to nanometer level control. However, modern pulse width modulation (PWM) amplifiers rival their performance with substantially greater efficiency and compactness. Direct drive linear servo motors have eliminated the mechanical imperfections of lead screw driven stages. Computational power has also mushroomed, permitting very high servo update rates and complex path calculations.
Measurement of Success
Our ability to achieve very high levels of precision motion control is due to an advanced suite of premiere metrology gear. The instruments we utilize include:
- Heterodyne laser interferometers with resolutions to 0.5 nanometers
- Homodyne laser interferometers with resolution to 39 picometers and +/- 10 nanoseconds timing
- Angle measuring interferometers with resolution to 1 nanoradian
- Precision Zerodur XY grid encoders (Figure 4)
- Precision optical reference mirrors in one and two axes
- Optical and electronic autocollimators with resolution to 1 microradian
- Capacitance and linear variable differential (LVDT) displacement sensors
- Dynamic Signal and Time Interval Analyzers, with timing jitter of +/- 25 picoseconds
- Pressure, temperature and humidity compensation sensors and software
Data is only meaningful when properly analyzed and we pride ourselves on a very strong bench of data analysis skills. We go deep into the data, both during application development and as part of each system’s Acceptance Test Procedure (ATP). During the development phase, our engineers use MATLAB and Mathcad to thoughtfully analyze the data and find the root cause of parameters that could threaten the meeting the client’s specifications. These are then turned into LabView graphical user interfaces (GUI) for our production team, automating both the motion and the data acquisition to quickly and reliably confirm that all units meet the client’s specifications.
For the highest level of performance, a laser interferometer is included as part of the positioning system. A laser interferometer is used to characterize the system at our facility, with residual stage errors corrected via stored compensation tables. With a two-axis laser interferometer, issues such as Abbe error can be cancelled at the customer’s point of interest.
For the highest level of performance, a laser interferometer is included as part of the positioning system. A laser interferometer is used to characterize the system at our facility, with residual stage errors corrected via stored compensation tables. With a two-axis laser interferometer, issues such as Abbe error can be cancelled at the customer’s point of interest.
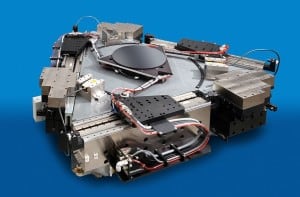
An example of what can be achieved with such thorough data gathering and analysis is Dover Motion’s Delta Stage (Figure 5). In this custom multi-axis precision linear stage, two plane mirrors at 60 degrees are diamond turned into the highly light-weighted, dip-brazed, 300-millimeter planar air bearing chuck-puck. The analog output of the interferometer axes was sampled with 14 bit depth at 10 MHz, providing a noise floor of about 3 picometers, and high performance double precision floating point routines handled all geometric and kinematic transformations. Both inertial forces and center of gravity shifts were nearly completely cancelled by design.
Additional Resources
American Society for Precision Engineering (ASPE) paper on the Delta Stage that Dover Motion developed.
ASPE paper on very high resolution systems.
We pride ourselves on being able to work with any specialized precision motion control requirements our clients have. Contact us today to learn how we can collaborate to configure the right precision motion control solution for your application.
Building the Right Precision Motion Control System
Dover Motion offers a variety of standard products for your precision motion control needs, and we also specialize in collaborating with our clients to configure the right motion solution for their unique application. With more than 60 years of experience in the life sciences, diagnostics, and factory automation industries, we understand your needs and industry and can provide you the flexibility you need to hit your cost and schedule targets. Contact us today to learn more about how we can help you with your next project.
Suggested Precision Motion Control Products
Precision Motion Control Products
The DOF-5™ microscope stage is optimized for objective focusing with increased travel, higher bandwidth, and lower cost than piezo stages.
wdt_ID | Travel | 5 mm |
---|---|---|
1 | Resolution | 1.25 nm |
2 | Repeatability | < 50 nm |
3 | Bandwidth | > 225 Hz |
The award winning SmartStage™ XY stage offers high precision and includes an embedded controller inside the stage.
wdt_ID | Travel | 50 - 200 mm |
---|---|---|
1 | Accuracy | ≤ 10 μm |
2 | Repeatability | 0.8 μm |
3 | Payload | 10 kg |